Extruders are widely used for a variety of conveyed goods in the food industry and the screws are usually ground and polished by hand, which is costly and time-consuming. Extruders move not only bulk goods but also viscous masses such as dough. A rough surface is prone to food residue and micro-organism deposits, which makes surface cleaning much harder. Additionally, sharp, unstable edges are problematic since they can repeatedly break off when under stress, leaving small fragments in the food. The only way to prevent this, and to guarantee uninterrupted production and food purity, is smooth, even surfaces in even the smallest angles, and rounded, stable edges. Typically, components used in the food industry are post processed in several steps, which can take several hours and is very costly. Since extruders can be heavy and unwieldy, the risk of injury from sharp edges is high.
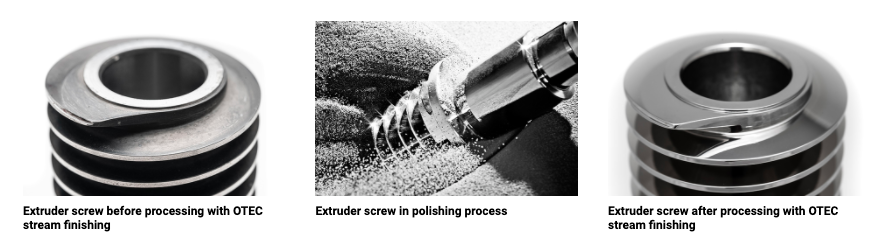
ACHIEVING SURFACE QUALITY EFFICIENTLY
The most efficient and cost-effective way to obtain evenly smoothed surfaces and rounded, stable edges is customized post processing using OTEC stream finishing technology: a mechanized, reliable, repeatable process for smoothing and edge rounding. Targeted, controlled processing ensures that the extruder screw can do its job unimpaired: no catching, no increased resistance and no deposit build-ups.
CASE STUDY: SCHAAF TECHNOLOGIE GMBH
Schaaf Technologie GmbH manufactures screw extruders. Manually post processing the parts after turning and milling used to take the company around four hours. Recently Schaaf Technologie replaced all of this manual processing with OTEC’s efficient stream finishing process.
According to Ron Hanke, Production Manager at Schaaf Technologie, “The OTEC stream finishing process means that we can process our screw surfaces automatically, evenly and consistently. The new process also improves tribological properties all-round, which in turn extends the service life of the parts by reducing friction. The process now takes just 30 minutes, and the time it takes for our employees to load the machine is minimal. We even obtain a better surface result than we did with manual finishing. The OTEC stream finishing process gives us a huge advantage in terms of both quality and time.”
OTEC’S STREAM FINISHING PROCESS
OTEC’s stream finishing (SF) process, which was developed in-house, is ideal for particularly complex geometries. Components are clamped in a holder and lowered into a rotating container filled with an abrasive or polishing medium. The workpiece is also rotated to produce an even finish. This makes it feasible to achieve highly refined surfaces with roughness depths of up to Ra 0.01 µm even on the most complex geometries – all without manual strain or risk of injury.
The enormous machining forces used in stream finishing can remove material faster and more precisely than any other type of surface processing. It is also easy to store and retrieve custom process programs, ensuring repeatability.
OTEC’s latest innovation, the SF-HP, can even process large and heavy workpieces with a diameter and length of up to 650 mm and a maximum weight of up to 200 kg.

DEFINE YOUR PROCESS WITH THE HELP OF OTEC’S EXPERTS
Work with us to identify exactly the right process for your components. Contact us today to request sample processing.