During the manufacturing of metal workpieces it’s often necessary to machine threads. Usually when workpieces have to be mounted or assembled to other parts, screw connections are unavoidable. Generally, there are two different ways to create threads: cutting (‘taps’), which is the most popular method, and forming (‘forming tools’).
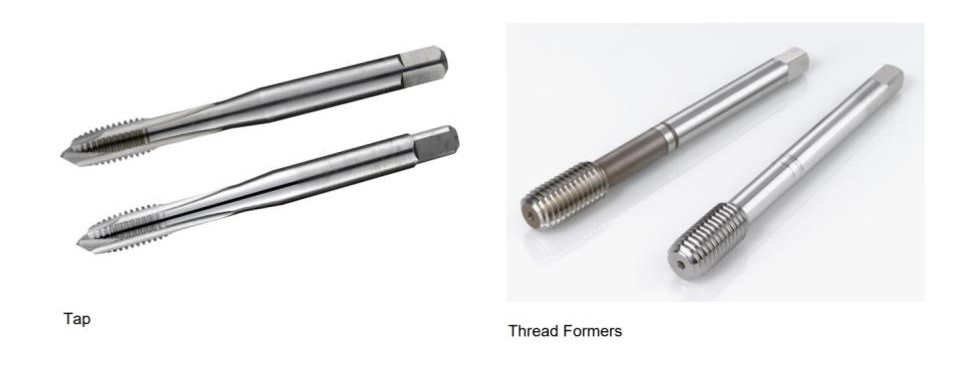
OTEC has developed several surface finishing processes of threading tools. With OTEC’s stream finishing machines with Pulsfinish, OTEC’s pulse drive, the tools can be processed reliably, quickly and economically according to the tools’ requirements. The principle of pulse finishing system is based on the precisely defined and rapidly repeating relative movement between media and workpiece. Here the clamped workpiece is immersed in the media stream of the rotating drum where it is quickly accelerated to a speed of over 2,000 rpm. Then it is decelerated and accelerated once again. The differing speeds resulting from the inertia of the media in the drum and the rapid change of workpiece speed give rise to an extremely intense and precisely controllable abrasive effect.
Compared to conventional processing methods, OTEC’s pulse finishing process has far fewer steps. Deburring, smoothing and rounding of the edges all happens in one step, which leads to both time and cost savings. A surface treated with the OTEC process also improves the adhesion of the subsequent coatings and extends the tool life.
When dealing with cutting tools, taps generally need a deburring process after tool grinding. With the conventional brushing method, all burrs can never be removed, which negatively affects the later coating process. Non-removed burrs break off and create uncoated areas that wear more quickly. With OTEC’s stream finishing machines with pulse drive (Pulsfinish), workpieces can be deburred within several seconds to several minutes.
Cutting edges can be rounded to a defined measurement. By setting the parameters container and workpiece rotation speed as well as the immersion angles the geometry of the taps can be modified in order to match the requested and optimal shape.
When processing forming tools, the main task is to evenly smoothen the entire tool surface. A smooth surface reduces the formation of material in the forming grooves and reduces the friction between the tool and the material to be deformed. Depending on the requirements, the defined rounding of certain functional edges is also necessary. By using a surface finishing process developed by OTEC, it’s possible to achieve these requirements. Compared to competing processes like shot blasting, the OTEC process is both cost effective and at the same time quite flexible, as it can be adapted to different workpiece shapes. Using this finishing process, the deformation forces can be reduced by about 60%.
OTEC’s stream finishing machines with pulse drive (Pulsfinish) make it possible to work with high energy and small and abrasive media. The finishing target is achieved in about one to two minutes, depending on the size of the tap and the requested result. The media used is also smoothing the surface of the tools, which improves the coating behavior and tool life. The process is very flexible and adapts to every dimension and shape of taps. OTEC’s stream finishing machines are highly cost effective since the wearing of the media used is low and additionally, a single machine is able to process a large number of workpieces at the same time.
Contact us today to request sample processing for your threading tools.