Cutter bodies such as drilling, milling and rotary bodies are used for machining processes and serve as holders for inserts. Cutter bodies are available in different lengths and shapes and are manufactured of hardenable steel from which the cutter body is first milled, then deburred, hardened and ground to size. Finally, the polishing or coating of the surface follows e.g. with hard chrome. The coating is intended to prevent corrosion, but is quickly removed by the chips produced during cutting.
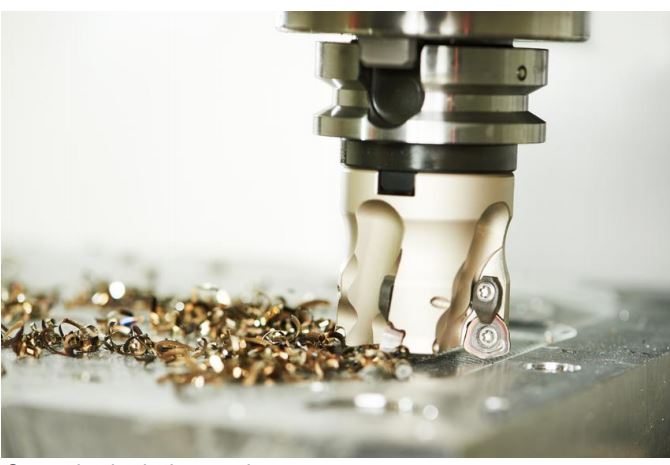
The deburring and polishing of cutter bodies has usually been carried out by brushing or blasting. The results obtained using this method are often inconsistent and inaccurate. For instance, if the contact surface for the insert is not absolutely flat, it will have a negative impact on the cutting process itself. Additionally, non-removed burrs can affect the stability during the cutting process. With OTEC’s SF series of stream finishing machines, tool bodies can be perfectly deburred and polished with repeatable and reliable results. In contrast to manual machining, OTEC’s stream finishing machines deliver consistently perfect results. Depending on the initial quality and the size of the workpieces, the typical processing times for polishing are between five to eight minutes. Thanks to OTEC’s patented pulse finishing technology, it’s possible to reduce an initial roughness from Ra 0.2 – 0.5 µm to Ra 0.03 – 0.05 µm.
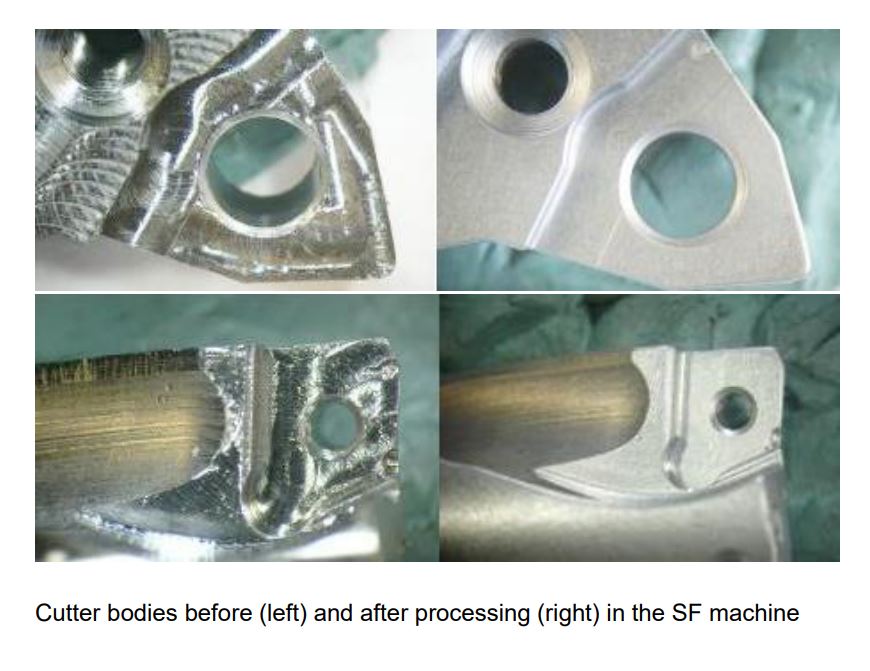
For surface processing, two main tasks are involved in the production of cutter bodies: Deburring after milling and polishing after hardening and grinding. The reliable removal of burrs is important for optimum fit of the inserts on the cutter body. A burr-free and flat support surface is important for stability during the cutting process and prevents chipping of the insert. The subsequent polish removes the oxide layer formed during hardening, thereby improving the visual appearance and upgrading the part for sale. The perfectly polished, smooth surface not only affects the appearance of the tool but also the functionality. Due to the polish, the surface is closed, compacted and significantly smoothed. The extreme smoothness offers less attack surface for corrosion and ensures a better chip flow in the flute. A specific surface treatment can thus significantly increase the efficiency of the cutter tool.
To learn more about OTEC’s stream finishing machines or request sample processing, contact us today.